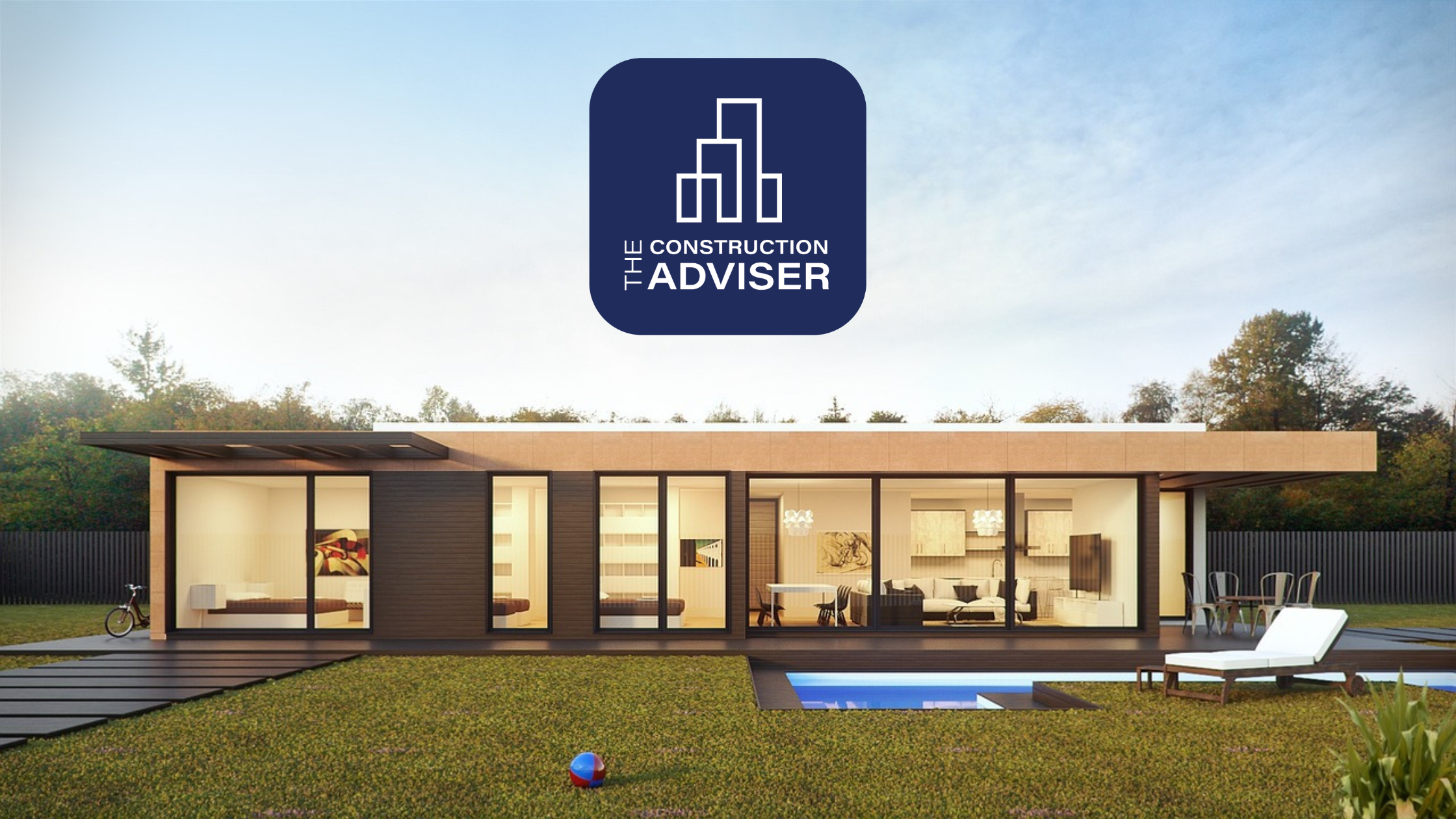
The future of housing is undergoing significant transformations, and one interesting trend is the rise of industrialised building systems. Imagine buildings where components are preconstructed in factories and then seamlessly assembled on-site. This approach not only offers cost-effective solutions but also reduces the energy footprint associated with traditional construction methods.
By integrating pre-built elements, homes become more efficient fabricate and install. The streamlined process not only saves time and resources but also ensures a higher level of precision and quality control. This method allows architects and builders to create structurally sound and aesthetically pleasing homes that are constructed efficiently and to a consistent quality.
Another notable advantage is the economic benefit. Industrialised or prefabricated building systems enable a quicker turnaround time, reducing labour costs. Wasted materials and minimising construction delays. Moreover, the controlled environment of a factory setting eliminates weather-related challenges, ensuring consistent quality regardless of external conditions.
Pre-built elements are not limited to residential structures, they are increasingly used in commercial spaces, government facilities schools, and healthcare facilities, transforming the entire construction process.
Prefabricated housing utilises materials such as steel, concrete, wood, aluminium, glass, plastic composites, insulation materials, and fibre cement. These materials are chosen based on factors such as budget, climate, design preferences, and functionality. Insulation materials are used for energy efficiency, and fibre cement provides options for cladding. The choice of material depends on the specific requirements of the prefab structure, supporting flexibility in construction methods.
Consider Singapore, a prime example of the successful implementation of industrialised building systems. The country’s public housing projects, such as the Punggol Northshore Residences, have embraced prefabrication techniques. This approach has enabled Singapore to address the demand for affordable housing swiftly and sustainably. While prefabricated building systems offer another option, they are not without challenges:
- The Initial Investment of implementing prefabrication technology requires significant initial investment in factory setup, technology, and skilled labour. Companies and governments need to invest substantial capital to adopt these methods.
- Design flexibility can be limited with prefabricated elements. Architects and designers need to work within the constraints of standardised modules, which might restrict creative freedom.
- Prefabricated components need to be transported from factories to construction sites. For projects located in remote areas, transportation costs can be substantial, affecting the overall cost-effectiveness.
- Prefabrication demands a skilled workforce knowledgeable about the assembly of pre-built components. Training existing construction workers or hiring specialised labour adds an additional layer of complexity.
- Building codes and regulations vary across regions and countries. Adapting prefabricated designs to comply with local regulations can be challenging and time-consuming.
- While prefabrication can enhance quality control in a factory setting, errors in design and/or construction can still occur, but the occurrence is vastly reduced. Ensuring consistent quality across all prefabricated elements is essential.
Addressing these challenges requires collaborative efforts from governments, industries, and research institutions to create standards, invest in research, and provide incentives for adopting prefabricated building systems.
As we move forward, embracing diverse options of these advanced building methods it will be vital in meeting the escalating demand for quality and affordable homes both here in Australia and worldwide.
To discuss further your construction needs please contact us at info@tcadviser.com.au
#FutureHomes #InnovationInConstruction
read more articles